Whether noise comes from an air conditioning system, a rotating fan, or any other device that creates noise through turbulent flows, the sound generation and propagation mechanisms must be addressed to satisfy the ever increasing customer quality expectations. These systems are often required to operate for extended periods of time. Even low noise levels can significantly degrade the comfort for the user. With Actran, engineers from all industries have tools to predict and understand how to design quiet workplaces, quiet car and aircraft interiors, or silent electronic devices.
Actran AeroAcoustics is a module that features advanced capabilities to predict accurate and efficient noise generation of turbulent flows. Results from an unsteady flow simulation performed with CFD codes such as Cradle CFD™, Fluent™, Star-CD™, StarCCM+™, Powerflow™, OpenFOAM™ and others are used by Actran AeroAcoustics to compute aerodynamic noise sources. The acoustic propagation from these aerodynamic sources are then computed to provide users with acoustic results such as noise levels and directivity.
Using Actran AeroAcoustics, the noise generated by any turbulent flow can be thoroughly predicted. Users can benefit from all features of the Actran software suite to study the interaction between the aeroacoustic noise sources and a vibrating structure, absorbent materials, or acoustic traps such as resonators.
Applications for Actran AeroAcoustics include rotating fans, air conditioning modules and side mirrors. It provides users with a complete understanding of the physical phenomena involved in the noise creation process.
Actran AeroAcoustics offers high performance solvers and parallel processing features with full integration in the Actran pre- and post-processing environment, Actran VI. It can also be combined with Actran VibroAcoustics in order to address aero-vibro-acoustic challenges such as side mirror noise.
Actran SNGR: Predicting the noise generated by complex flows from steady CFD solutions
Use this module to predict the noise generated by turbulent flows from steady CFD solutions. Actran SNGR recovers aerodynamic noise sources from flow simulations performed with CFD codes such as Cradle CFD™, Fluent™, Star-CD™, StarCCM+™, Powerflow™ or OpenFOAM™. The results from an steady flow simulation obtained from a RANS CFD analysis are used in the Actran SNGR to synthesize the noise sources. These sources are then imported into an acoustic computation and are then propagated. Actran SNGR allows addressing the noise generated from turbulent flows in a much faster way than classic aero-acoustic approaches and it is specifically useful when relative levels between different designs are needed such as in optimization loops.

Sample applications:
- Air conditioning modules (HVAC)
- Side mirror noise
- Airframe noise (landing gear, trailing edge)
- Air distribution systems
Actran TM: A powerful acoustic CAE tool for turbomachinery noise prediction
Use Actran TM to analyze the sound radiated by turbomachinery and to optimize the related acoustic treatments. One of the challenges of acoustic CAE methods is handling of large models associated to high wave number and to large geometrical size and complexity. Actran TM provides efficient solver technologies to address this problem, which includes advanced parallel processing.
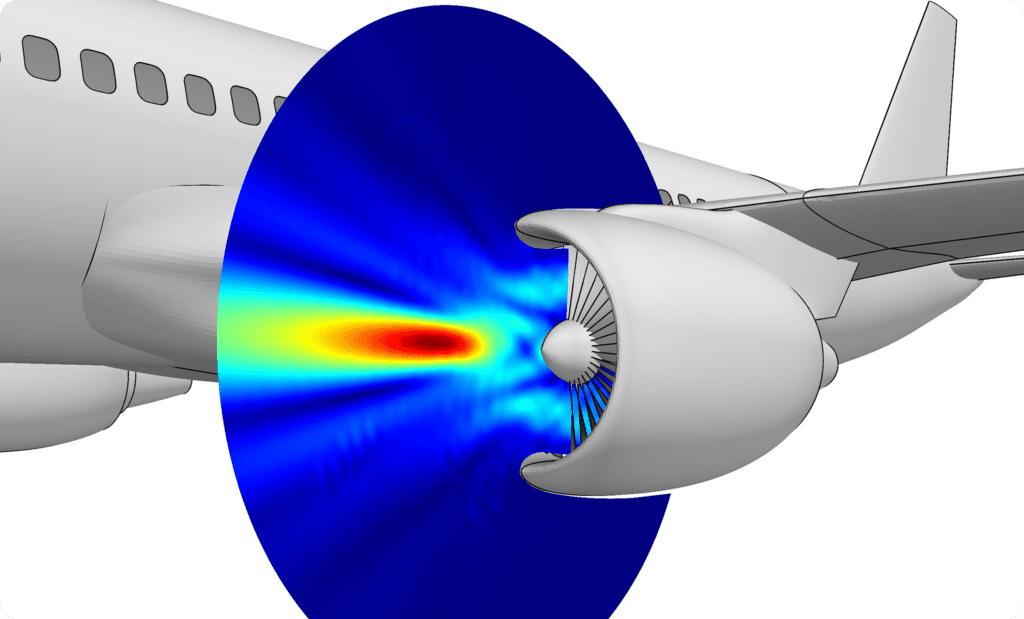
In addition to studying aircraft engines, Actran TM can be used to analyze inlet and outlet liners for turbine engines, environmental control systems, and auxiliary power units, and for non-aerospace applications like computer cooling systems. Actran TM can be complemented by Actran DGM to solve problems involving complex shear layers and flow gradients occurring at engine exhaust.
Sample applications:
- Aircraft engine noise, including nacelle design
- Ducted cooling systems (electronic devices)
- Blower systems (air conditioning modules)
- Turbine noise
Actran DGM: Model noise propagation in complex flows
Actran DGM solves the linearized Euler equations using discontinuous Galerkin method and is
used for predicting the noise in complex physical conditions. It is particularly well suited to
solving aero-acoustic problems at the exhaust of a double steam turbofan engine, including
effects such as propagation through strong shear layers, high temperature gradients and
non-homentropic mean flows.
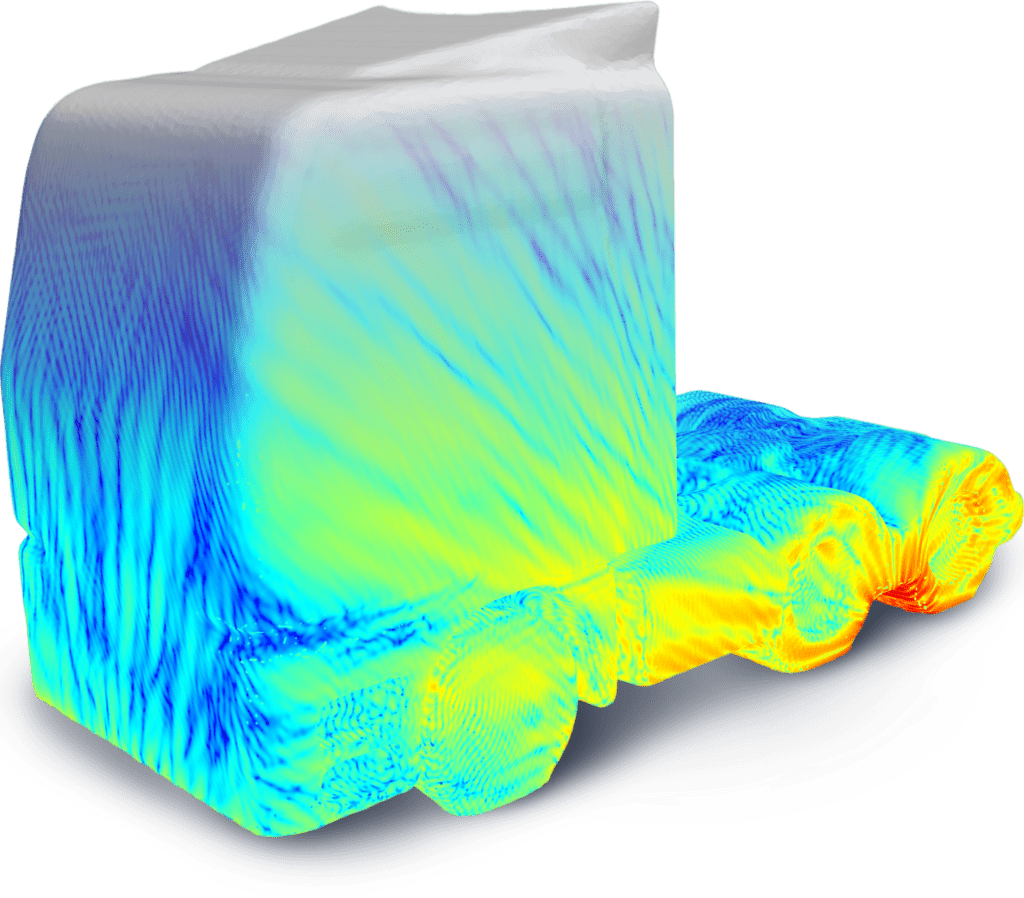
Actran DGM uses unstructured meshes, and is not constrained by standard limitations of
finite difference methods. Due to its discontinuity property, the mesh can be non-conformal
with no impact on the accuracy and efficiency. Furthermore, this allows to combine very
small and large elements in a single mesh, and the order of the elements is automatically
adapted.
Sample applications:
- Exhaust of turbomachines
- Inlet of large turbomachines
- All acoustic propagation problems with non-homogeneous mean flow conditions